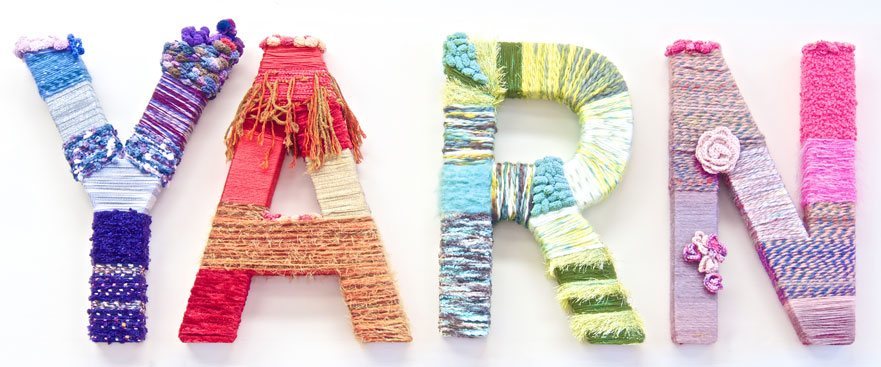
Initial Cost
Fire to order given by your customers, you can prepare initial cost by determining profit, wastage and commission rates. You can access easily thanks to filter that by archiving based on costs, yarn, date and customer of made. Initial cost you prepared is relatable with any lot.
Receipts information belonging to yarn are transferable automatic to pro forma cost screen. With Xerography, you can make easily new cost preparation transaction by made carrying from initial cost card your prepared.
You can make profit analysis automatic on yarn initial cost table. You can access automatic receipt belonging to fabric on screen. You can track made all cost working belonging to yarn on receipt.
You can make cost according to different type of currency. Cost working is updatable single or collective according to changing currency and price.
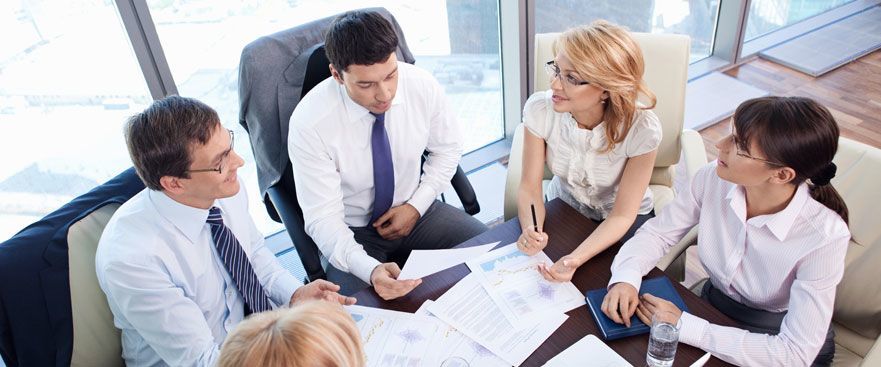
Customer Order Management
You can enter detailed customer order information. Lot number, color code and produce process are representable in customer order entry. You can follow up orders’ manufacture state (lot, shipping) in business. You can follow up open-closed order distribution based on inventory and current account. Customer orders can transferable automatically to work order. On customer order, you can access lot information.
You can follow up order distribution based on customer, inventory and color. You can prepare automatic purchase and sub-contractor instruction on customer order.
You can access work order on ordering. You can block to interfere to work order and ordering of creating with work order. Not creating work order for ordering, you can make number assignment of work order.
You can associate with documents related to order and you can provide to access on request. You can access order, sales and cost analysis information belonging to yarn.
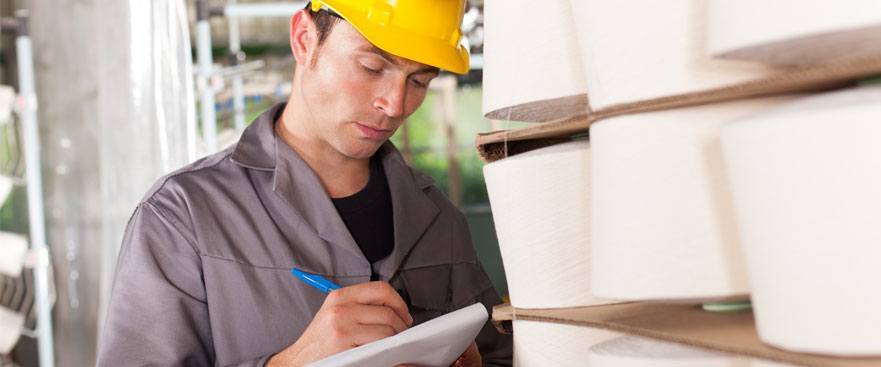
Work Order Follow Up (Lot Card)
You can define all information belonging to manufacture in detail. You can prepare automatic work order from customer order and receive work order documents with barcode or manual. You can define private sphere of company on work order.
You can make more than one lot (companionship) card design.
According to customer lot number, you can follow manufacture stages. You can define unlimited work flow process and can follow up repair lot (interior/exterior).
You can define manufacture detail information based on yarn on work order. Different products, you can follow up same work order.
You can follow up detailed any manufacture movement belonging to order and lot in lot order history.
You can divide lot to sub-lot of production at any stage. You can follow up on single a form movements belonging to lot.
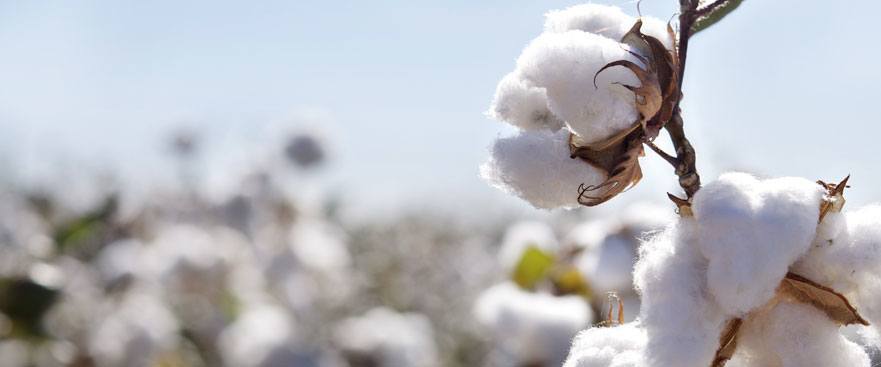
Raw Materials Requirement
You can calculate your need raw materials by defining wastage and raw material usage rate on card. You can give automatic purchase order in accordance with determining needs or customer order.
You can make needs planning and give purchase order.
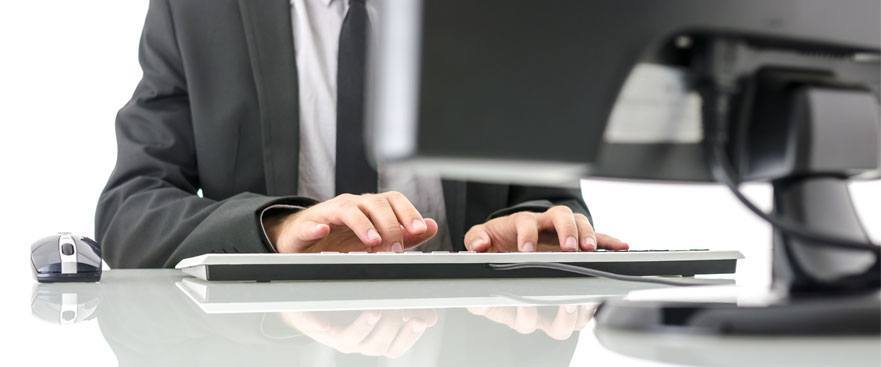
Purchase Management
You can enter detailed purchase order information.
You can give automatic purchase order in accordance with customer order. Purchase order can transferable on dispatch list. You can define optimal and critical inventory amount on inventory. You can give an order automatic by accessed on one screen of inventory under critical inventory amount.
Open-closed order distribution, you can follow up based on inventory and current account. You can receive detailed reports based on customer, supplier and inventory.

Serial Follow Up
You can produce automatic roll card on lot card and can define roll card in detailed. You can receive barcoded documents including errors belonging to roll card.
Defined roll card can transferable to delivery note. You can prepare barcoded product label.
Thanks to scales connection, you can receive amount information belonging to serial on scales. You can make data definition based on serial so you can provide to calculate net amount automatically.
You can make serial division and integration transaction and unlimited label definition.
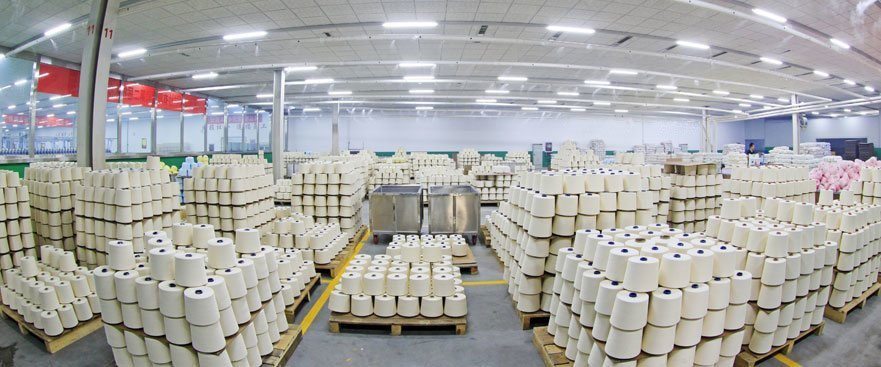
Warehouse Management
You can follow up customers’ yarn and fabric inventory based on warehouse. You can follow up reserve and free inventory thanks to allocation transaction. You can follow up your inventory by being variant (color-lot number etc.)
You can follow up return transaction based on warehouse. You can use based on dispatch note by making return transaction and follow up amount.
Inventor is relatable manufacture transaction.
You can follow up based on intended (lot, variant, producer, date etc.) state of warehouse your inventory. State of inventory can traceable by being variant based on work order (lot).

Production Planning
You can do planning on the basis of machine/work order. You can display all lot on one monitor. You can do planning machine on sheet on the basis of hour. You can see 24 hours’ production status of your business.
You can prepare production instruction schedule for your business.
You can access to all opened lot cards until this day and you can see these cards’ lot status at previous dates. You can follow up lots’ all production processes in detail. You can follow up current situation of your business on business status screen.
You can create machine groups and you can separately follow up these groups on planning and production forms.
You can process standard times (process, machine, product group, etc.) in detail.
You can calculate automatically information of planning, exit, date and hour on the basis of standard time information.
You can do collective planning belong to processes through planning list screen. You can change easily planning information (machine, date etc.)
You can transfer automatically to next days uninitiated production planning records.
You can control capacity of machines while planning. For the planningrecords that collide with each other you can make the time information automatically set. By creating operation machine groups, you can prevent operations from being assigned to wrong machines.
You can prevent lot from being assigned to external processes other than route. You can get reports of lots which are planned but you didn’t start manufacturing. You can get reports that compare planning and manufacturing information.
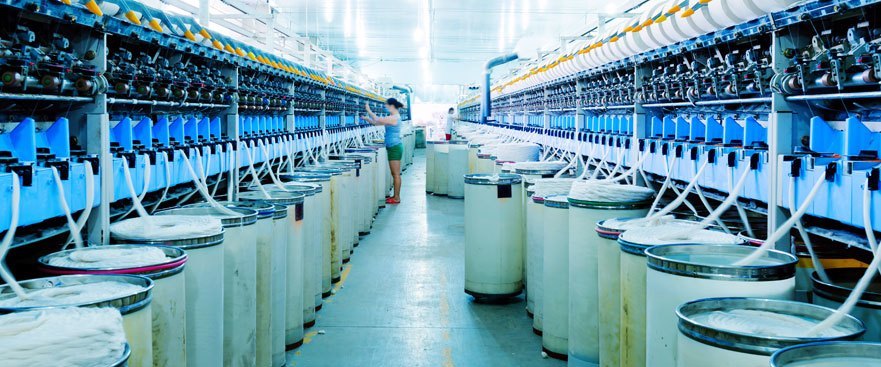
Production Follow Up
You can do detailed sub-contractor (dye, printing, washing up etc.) follow up. You can follow up internal and external production processes in terms of lot. You can prevent wrong stock movements by making manufacturing movements on the basis of lot number.
You can do sub-contractor follow up on the basis of lot. You can get detailed and cumulative reports in terms of lot. You can follow up the subcontractors’ lots opened/closed.
You can get detailed reports by following up products that go to and come from production returning and loss rates.
You can follow up relative and general raw material movements that are in the process of production. You can follow up raw material remained after production.
You can do detailed follow up by reaching the sub-contractor card via voucher. You can get reports of daily production situation, sub-contractor follow up and lot/order.
You can get barcodes of work order, records and machines.
You can measure staff and machinery efficiency in the direction of the times that you will determine.
Thanks to its parametric structure, you can follow up detailed information about production. Through barcoded production machinery, records and production situation can be followed up.
Via route control you can prevent wrong production movements from emerging and enable production to continue healthily. Through route control, you can follow up only certain operations in terms of process. By creating process machinery groups, via the control of process machine compatibility you can enable manufacturing information to be created right and healthily.
You can prevent a machine from getting a new production input while continuing producing. By creating special barcode structures, you can produce information of additional processes without interfere in the route card.
You can follow up the information of group lots separately or together. You can stop delivery of the lots that don’t come out of the last process. You can report lots’ current production situation and future production stages.
You can follow up time waste and stopping information of machines in detail. During production, you can print barcoded/not barcoded forms in detailand you can enable detailed information of work order and production to be outputted on the form. You can divide production and fason movements in process into different lots. By this, you can follow up order loss values healthily.
In the direction of your daily production and recipe knowledge, you can make automatic waste activities.
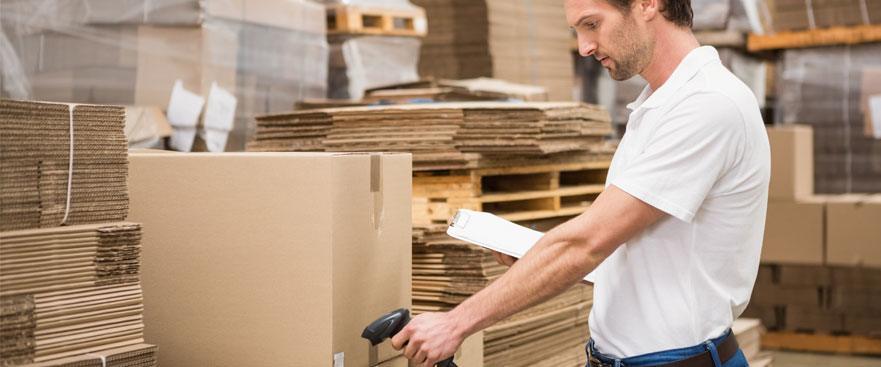
Delivery and Invoicing
You can carry out your customer delivery on the basis of lot and order. You can make delivery planning by choosing which lots will be delivered to the customer. By getting the delivery planning report, you can give an order to the depot.
You can make the inventory receipt out of lots’ production completed. You can enable the losses to be automatically calculated by typing into the lot’s exact values. You can get the lot’s exact values from the serial card.
In order to subtract the losses from the store, you can make out an automatic invoice of the loss. You can design an invoice of delivery as required.
You can do the operation of closing automatic work order. You can prepare automatic dispatch note from the lot. You can define the work order information on the inventory receipt. You can prepare weight lists.
You can get delivery reports as required (customer, stock, day, week, month etc.) You can make bill connections you can reach the delivery dates belonging to the lot. With the weighing machine connection, you can transfer the amount of the delivery automatically to the delivery invoice.
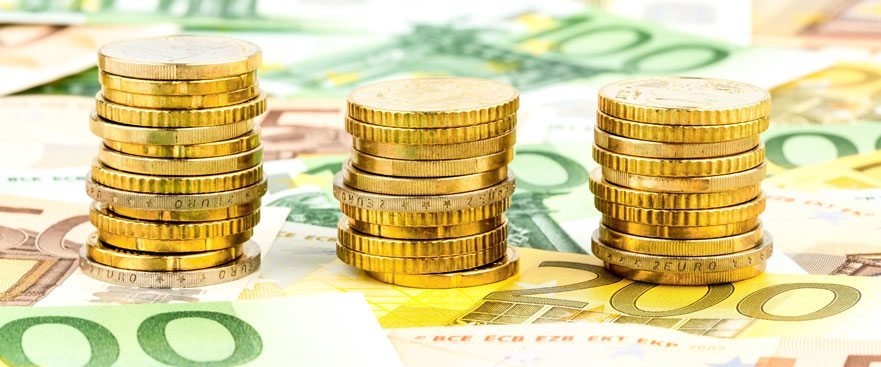
Cost
You can automatically calculate the real cost. You can get the lot/order cost automatically. You can make income-expanse and profit-waste analyses. You can get the initial cost and real cost table comparatively in terms of lot.
You can get cost reports on the basis of currency and Turkish lira. You can make static and general characterization (deploy) on the basis of lot. You can compare the costs at every stage of production to prime cost.
You can follow up group lots’ cost separately or together.
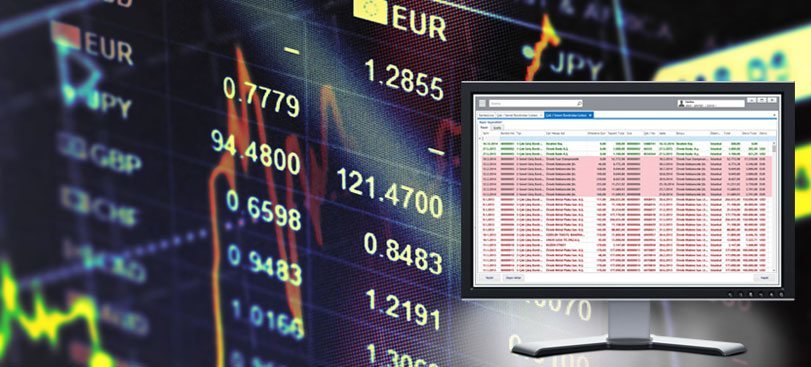
The carried risk your company is measuring accurately in increasingly growing competition conditions, it will ensure you that taking necessary measures and using your financial resources more efficiently.
The importance of finance management is growing day by day, which is the key point of making your company's decisions to reach success.
Finance Managers can accessible easily the data analysis they need related to predicting the future and past evaluation, taking all financial decisions with investments or financing for capturing rationality and giving the right decision.
At the same time Sentez LIVE ERP Finance Management provides you all the necessary data such as in the matter of analyzing the finance of your company, evaluating the result of your company’s actions, making plans and directing the resources to the right areas.
The using of a more comprehensive financial decision-making model become a necessity for continue existence with balanced growth and appropriate business’s goal in your business’s adverse economic conditions.
Financial data, not only effective in board of directors financial decisions also effective in marketing, manufacture, human resources, R & D and all strategic decisions about the company.
The decisions taken for increasing the profitability also increases the risks. Effective and successful financing management has a big and important roll, especially in short-term investments.
Need of financial statement and reports can prepared and trackable with flexible reporting and tracking system.
LiveERP provides to fulfill the requirement national and international to all financial.
Your company will be adapted to changing market conditions thanks to definable and customizable risk calculating methods.
LiveERP ensures doing your operations by using different currencies. It also ensures you calculate the amounts entered in local currency or exchange automatically as transaction exchange.
It ensures you to follow up the balances of current accounts from different exchanges.
It ensures you to determine different exchanges for reporting. It ensures to report the amounts entered in local currency or exchange automatically as transaction exchange.
It ensures to make healthy payment-cash proceeds plan thanks to detailed definitions based on payments’ and cash proceeds’ maturities.
It ensures you to make matching based on payment-cash proceeds plan based on document. It also ensures you to use different exchanges on matching operations.
It ensures you to calculate delay interest and reflect to accounts when it is necessary by controlling payment and cash proceeds based on payment- cash proceeds plan according to their maturity.
It ensures to calculate and reflect to account automatically the changing positively and negatively direction of exchange rates according to local currency within time of change operations.
It ensures you to take under control your cash flow thanks to the detailed debt tracking report and analysis.
It ensures you to transfer bank operations automatically with available data transfer services.
It ensures you to create your cross operations error-free thanks to operation transfer services between your companies Also ensures to transfer a document registered as sales document for your company to your other company as purchase document.
It ensures being effective, while calculating the risk of current account and follow up received warranty and given warrant through warranty management.
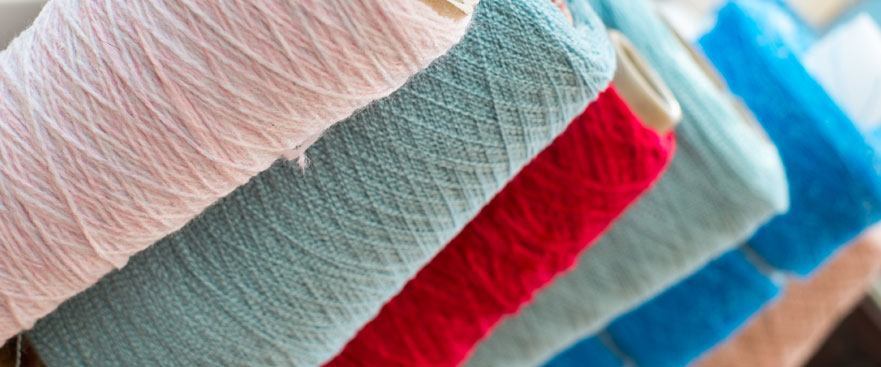
With increasing competition, only exact data collection is not enough for quick decision and put into practice. To business’performance increasing, exact report, exact analysis and indicator board must to be implemented.
SentezLIVEERP Business Solutions Platform was designed as business intelligence system contains whole modules.
It ensures necessity information for taking essential decision, right time of every user’s in accordance with system role.
It ensures through reports, analysis cubes and display panel according to information flow’s structure.
When user notice creating problem, user can examine in detail and interference to problem annihilation.
Primary Features
Easily Access
Easily Usage
Flexible, Reliable Structure
Working on Desktop, Mobile, Internet/Intranet
Variable Visual Design
Reports
Analysis
Control Panel
Analysis Cubes
25.5 K +
Satisfied Live User
SentezLİVE ERP platform has been beginning to be preferred by many institutions that by increasing with 25.500 users’ number of worldwide. Comparing to other ERP software, higher performance and lower cost advantages have been effective for preferably.
Please complete
the following form and one
of our representative will contact you.
+90 212 452 1515
Hürriyet Street No:5 Şirinevler
Bahçelievler, İstanbul
Show the Map